The Significance of Quality Management in the Life Sciences Industry and how to evolve it.
In the dynamic and highly regulated Life Sciences industry, effective quality management plays a crucial role in ensuring compliance, efficiency, and overall success. The integration of quality management systems within Life Sciences companies has been greatly facilitated by the implementation of SAP standard functionality, which has been widely adopted and proven over the years. However, industry specific requirements for Life Sciences companies were often addressed via extensive developments or 3rd party systems.
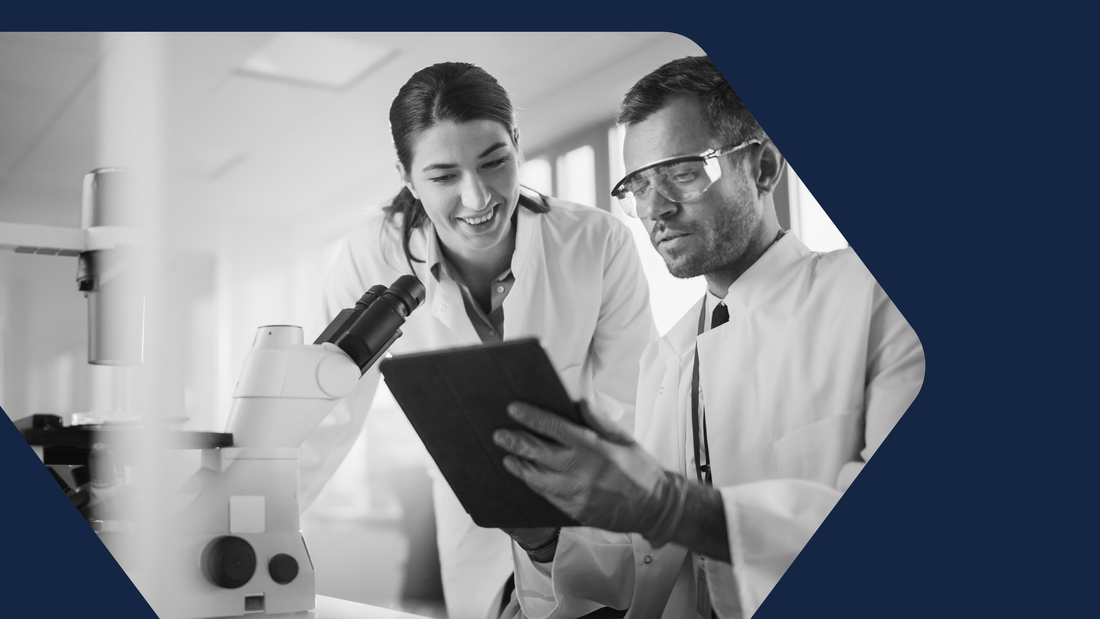
Companies have made significant investments in SAP QM with ECC, leveraging custom GUI screens, Web Dynpro, and Fiori, while relying on SAP standard functionality in the background to address known gaps. With the current transition to SAP S/4HANA, organizations are seeking new solutions that offer maximum benefits and enable them to optimize their quality control (QC) activities, streamline laboratory processes and providing additional functionalities for quality assurance (QA). At Tenthpin, we aim to highlight some of the most important criteria to consider in this process.
Seamless Integration in ERP landscape
One of the key criteria in achieving effective quality control is the seamless integration of quality assurance (QA) and quality control (QC) processes within your organization's ERP landscape and end-to-end pharmaceutical supply chain processes. By ensuring a smooth alignment between these two critical areas, businesses can streamline their operations, improve their Quality Management, and enhance regulatory compliance.
Integration with Non-ERP Applications & Laboratory Equipment
By integrating LIMS and LES functionality with the ERP, organizations can reduce data transfers, reduce manual interventions, and minimize the risk of errors or discrepancies. This integration promotes a streamlined and reliable quality control process leveraging existing technologies and capabilities. Integration of laboratory equipment is another aspect that enhances the effectiveness of Quality Management.
Streamlined Processes for QC and QA
Many companies want to reduce the paper-based documentation processes in the laboratories to increase operational efficiency. This requires documenting and tracing of samples through its entire lifespan in one central system with specific front ends, which are highly configurable, easy to use and provide all frequent activities out of one single screen. With such apps in place, organizations can significantly reduce the effort and minimize the risk of errors along the execution of test activities and data entries performed in the labs. This results in increased productivity and allows the teams to focus on value-added activities.
Efficient Labeling for Compliance
Efficient labeling processes further contribute to operational efficiency and compliance. By utilizing barcode label printing directly from the ERP system, organizations can optimize sample management, expedite sample identification, and ensure traceability throughout the entire lifecycle. This integration eliminates the need for complex interfaces and simplifies the IT landscape.
Transparency through Real-time Monitoring
Transparency is essential not only in maintaining high-quality standards, but also in maximizing business value. Implementing robust monitoring mechanisms, such as intuitive dashboards, enables real-time tracking of key performance indicators (KPIs). This empowers decision-makers to make data-driven decisions, identify areas for improvement, drive continuous enhancement and maximizes ROI.
“By aligning processes, leveraging automation, promoting transparency, and utilizing existing resources, organizations can achieve optimal quality control outcomes and stay ahead in today's competitive business landscape.”
Stefan Kubick, Partner, Tenthpin Management Consultants
Focus on Business Benefits
On one hand, it is important to meet functional needs and maintain the digital core, while on the other hand, the value side must be considered. Which features are crucial for the business, and how important is speed and agility versus completeness and depth? It is important to set the right priorities and create an appropriate roadmap.
Conclusion
In conclusion, integrating quality assurance and quality control seamlessly within the ERP landscape brings several benefits, including streamlined operations, improved product quality, enhanced regulatory compliance, and increased efficiency. By aligning processes, leveraging automation, promoting transparency, and utilizing existing resources, organizations can achieve optimal outcomes in QC and QA and stay ahead in today's competitive business landscape.
How to Realize Optimized Quality Management in Practice?
In practice, there are different approaches to achieving optimized Quality Management, depending on the unique situation of each company. While the standard SAP QM module may be sufficient for some, others may benefit from a combination of SAP with specific third-party applications. In response to the needs of certain companies, Tenthpin has developed a powerful new solution: Tenthpin Quality Management Evolved (T/QME). To learn more about this innovative solution, please visit https://tenthpin.com/digital-impact/quality-management-evolved